
VERICOR NEWS
STAYING UPDATED
and the gas turbine industry.
Celebrating 400,000 operating hours with BJ Energy Solutions and TITAN Technology Powered by Vericor TF50F gas turbines
Congratulations to BJ Energy Solutions on achieving an extraordinary milestone—surpassing 400,000 cumulative operating hours in hydraulic fracturing with the groundbreaking Direct Drive TITAN te...
Introducing the New 4 MW Mobile Genset, Dragon PowerGT43, Powered by Vericor© ASE50B Gas Turbine: A Game-Changer in Power Generation
Vericor Power Systems has once again raised the bar in mobile power generation with the launch of the Power GT43, a 4 MW mobile genset developed by Dragon and powered by ASE50B gas turbine. At...
Announcing Our 4MW Vericor Gas Turbine-Powered Mobile Generators
Houston, Texas, July 2, 2024/ -- We are excited to announce that our new 4 MW Vericor gas turbine-powered mobile generators are in the final stages of completion and are scheduled to begin accept...
US Navy LCAC Program: Honoring Us with Their Visit to Vericor Manufacturing Plant
...
Japanese LCAC: A Source of Pride in Earthquake Relief Efforts
...
Sojitz Executive Vice President Visit Vericor Manufacturing Plant
...
STAY CONNECTED
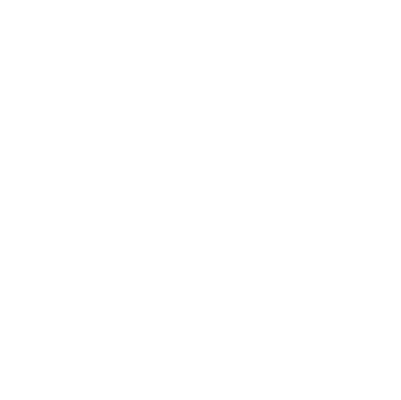
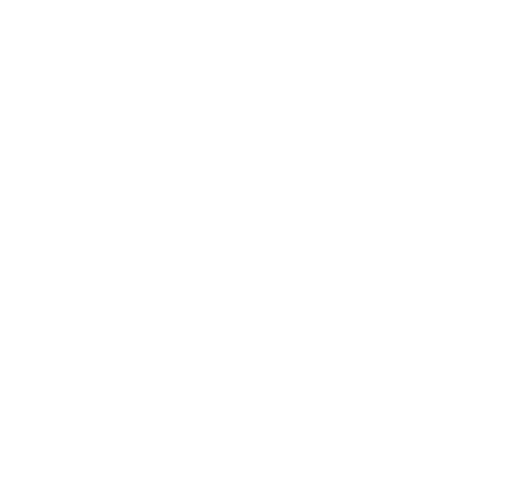